H3ロケットの打ち上げ失敗は残念でした。
どうやらH2までは試射をしていたようなのですが、H3はいきなり本番だったのですね。
自動車業界で言うところの「試作レス」というヤツです。
今回の結果について色々意見はあると思いますが、誰も失敗したくてしてるわけじゃないし、万全を期して望んでいると思うのです。
でも失敗は起こります。
万全を期しても失敗は起こる。
なぜかというと、失敗とは想定外だからです。
やってみなければ分からないこと
これはすなわち想定の外にあることなわけで
それを想定しろというのは大変難しいことです。
今回のような新型ロケットは新しいチャレンジなわけで、やってみないと分からないことだらけなのでしょう。
それらを何とか想定しながら開発を進めるのだけれど、とはいえ「想定に基づいてやる」ということは可能性の話なわけで、最終的にはやはり「やらないと分からない」というところに行き着くと思います。
そういうのを繰り返しながら技術は進歩していくわけで、そういう意味ではH3ロケットは、新たな一歩を踏み出したわけですね。
ひょっとしたらそういうのは、便利で豊かな生活の弊害と言えるのかもしれませんね。
物心がついたときから出来の良い工業製品に囲まれて、自らものを作らずとも、お金を払えば完璧(と思える)製品を難なく手に入れる生活をしていたら、こういう失敗に対して簡単に批判したり悲観的になったりするのかもしれません。
日本のロケットというと、大したことないのだろうなんて思われがちかもしれません。実のところ私はそう思っていました。
が、実はロシアのソユーズより大きくて能力が高かったりするので結構なものなのですよ。
なので恐らく能力的には有人の打ち上げは可能なのでしょうね。飛行特性とか本体や付随の設備的には難しかったりするのかもしれませんが。
あと興味深いのは使用された部品です。
H3では自動車用部品を使用したとのことです。
単に量産部品を流用したわけではなく、高いレベルの検査や試験の基準をクリアした上での採用となったとは思いますが。
これまで自動車業界、ことレースの世界においては、航空宇宙のテクノロジーを利用するのがよくある話でしたが、それが逆の流れになったわけですね。目的はコストダウンでしょうけど。
それにしても、この流れは興味深い。
技術は高いところから低いところへ流れるものですが、今やその高低の基準がコストということになっているわけですね。
加えて、日本の自動車業界の技術レベルは、今や宇宙機に採用されるレベルになっていると。
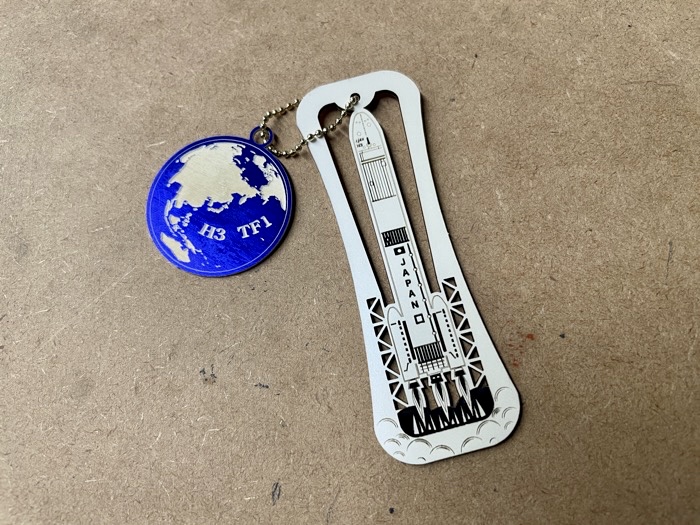
ロケット本体に、NIPPONではなくJAPANと文字が入ったのはH3からなのだそうです。
国際的な営業効果を考えてのことのようですね。
だからこそ低コスト化が競争力として重要だということです。
次回こそ成功して欲しいですね。