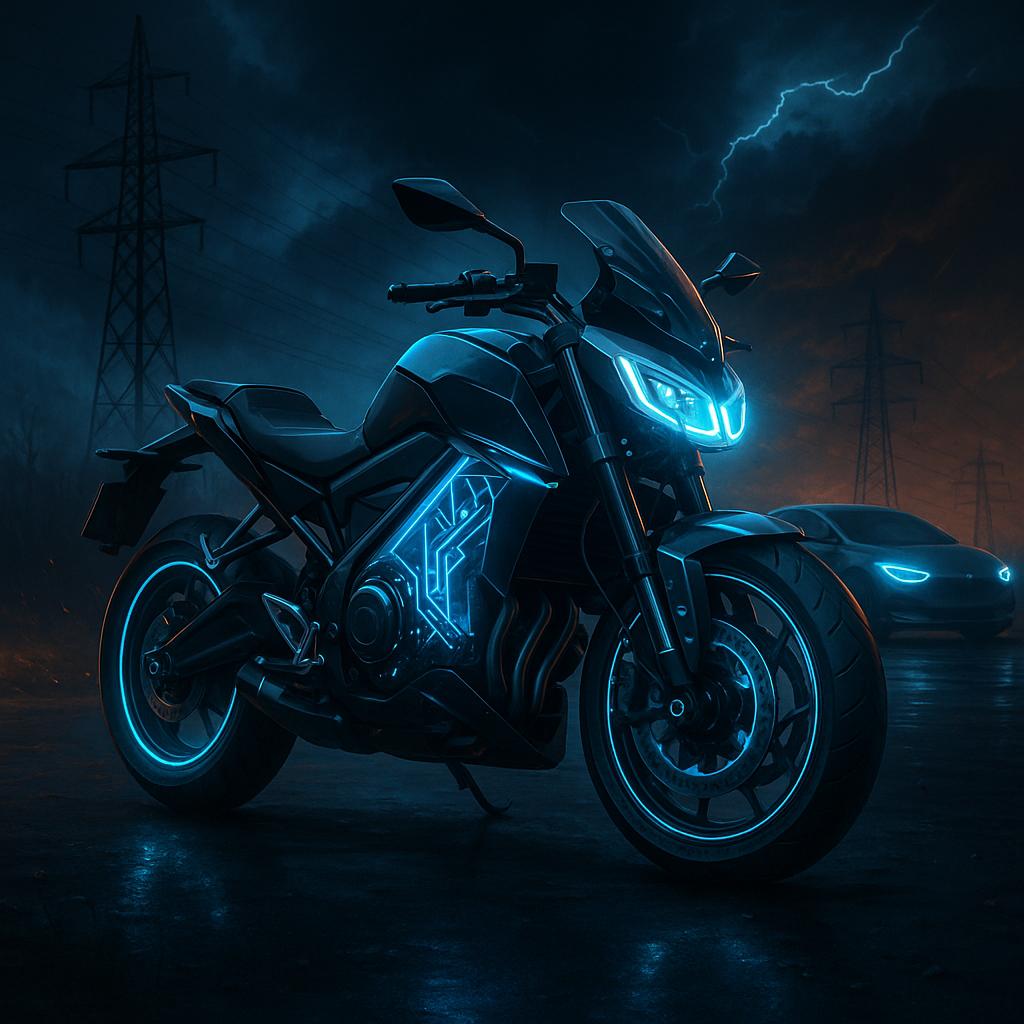
クルマのEV化、思ったほど進みませんね。
まぁ、電動化したところで、エネルギー源である化石燃料から走行までの最終効率は数パーセントしか変わらないし、製造に要するエネルギーや電池のリサイクル、そもそもの電池を巡る問題やらがあって、当初の思惑通りにはいかないってところでしょう。
それはそれとして、実は私、エンジンは好きだけど、別に電動モーターが嫌いなわけでもありません。
まぁ、乗って楽しければ良いかな、とも思いますし、パワーソースが何であれ、それぞれメリットはあるわけで、一概に良いだの悪いだのは言いにくいですから。
とはいえ、趣味のバイクが電動化されていったらどうなんだろうなぁ、なんてことは考えるのですよ。
最近は新しい電動バイクの話も聞かなくなってきましたけどね。
小さいのはあるようですが、それも主に国外の話ですね。
最近は、1日で1000キロ越えのツーリングなんてしてるけど、そういったことはできなくなるんだろうなぁとか、バイク自体重くなるんだろうなぁとか。
以前やったオーストラリア縦断なんてできなくなるでしょうね。
途中でマメに充電するなんてできないでしょうし。
そういうのは寂しいなぁ。
加減速の少ない高速域の連続走行では、回生充電もできないので、大した距離は走れないでしょうしね。
バイクEV化のメリットは何だろう?
静かなことや、獰猛な加速…あとは何かあるかな?
環境負荷は、実は大して変わらないと思うし。
車重もトルクも大きけりゃ、タイヤやブレーキなどの消耗品のライフは短くなるだろうし、重い乗り物は、乗るのが億劫になるんだよなぁ。
そうなったら乗車時間は減るわけで、環境負荷は低減されるとも言えるのか。それは皮肉だ。
全固体電池とか、電池の革命みたいな事が起きて、エネルギー密度が今のリチウムイオン電池の100倍くらいになれば、つまり現状の電池と同体積と重量で、100倍くらいエネルギーが突っ込めれば、エンジンと同じような使い方ができるのでしょうけどね。
充電インフラも気になる点ではあるなぁ。
大型連休など多くが充電を必要とするときに、乗用車と一緒に充電待ちをする絵を思い浮かべると…ちょっと微妙な感じです。
気に入った電動バイクがあるとして、何年も乗った末にバッテリー交換したくなったら
「あぁ、そんな古い型の電池なんて無いよ」
と言われてお終い?
まぁ、そんな頃まで生きてないだろうから気にすることでもないか。
と、今のところデメリットが多いのかなぁとか、そんなことを考えながら、技術の発展も楽しみにしてたりするのです。